PRESSING
Press machines use pressure to create or change the shape of metals used in manufacturing. Press machines use three different methods of processing metal: mechanical, hydraulic and forging. Applied pressure is used to cut or shape sheet metals. In addition, some press machine can punch holes in materials. Manufacturers use different types of press machines to build automobiles, airplanes and other vehicles and metal structures.
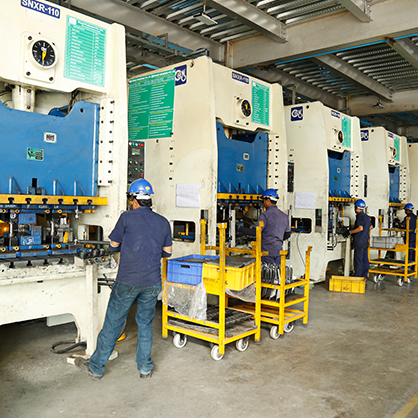